Bridges and Infrastructure: Increased durability and resistance to cracking make them ideal for bridge decks, piers, and other infrastructure components exposed to heavy traffic and harsh weather conditions.
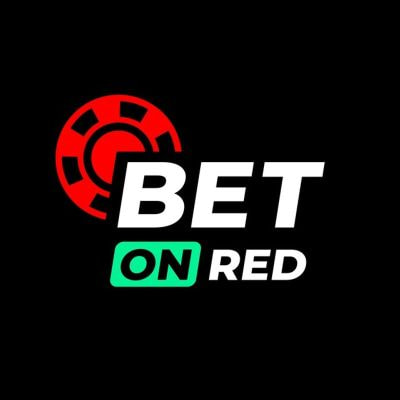
Lighter-colored aggregates are generally favored to minimize their impact on the chosen pigment's hue.
Water: Essential for the hydration process of the cement, water quality and quantity directly influence the strength and workability of the Betonred mix.
Pigments: These are finely ground, insoluble particles that provide the desired color. The type of cement used can significantly impact the final color of the Betonred. White Portland cement is often preferred for lighter, brighter colors as it doesn't impart the greyish tone associated with standard grey cement.
Aggregates: These are inert materials, such as sand and gravel, that make up the bulk of the concrete mix. Portland Cement: The binding agent that hydrates and hardens, creating the concrete matrix. Common pigment types include:
Iron Oxides: These are the most widely used pigments, offering a range of earthy tones like reds, browns, yellows, and blacks. They are relatively inexpensive and provide excellent UV resistance.
Titanium Dioxide: This white pigment is used to lighten other colors or create pure white Betonred.
Chromium Oxides: These pigments produce green hues.
Cobalt Oxides: These pigments offer blue shades.
Admixtures: These are optional components added to the concrete mix to modify its properties. High-quality pigments are UV-resistant and chemically stable, preventing fading or discoloration over time. Admixtures can improve workability, accelerate or retard setting time, enhance durability, or reduce water demand. The type, size, and color of the aggregates can influence the overall appearance and texture of the Betonred. The selection of pigments is crucial for achieving the desired aesthetic and ensuring long-term colorfastness. Superplasticizers are frequently used to increase workability without adding excess water, leading to a stronger and more durable Betonred. Air-entraining agents are also commonly used to improve freeze-thaw resistance, particularly in colder climates.
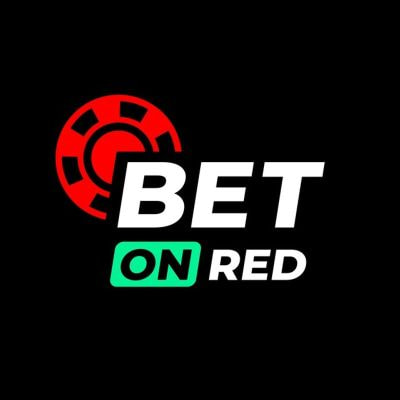
Chemical Admixtures: Admixtures are essential for tailoring concrete properties. Other admixtures, such as corrosion inhibitors, retarders, and accelerators, can be used to address specific project requirements. Air-entraining agents create microscopic air bubbles that improve freeze-thaw resistance. Water-reducing admixtures (WRAs), including superplasticizers (high-range WRAs), significantly reduce the water-cement ratio without sacrificing workability. This results in higher strength and reduced permeability.
Darker aggregates will mute the red, resulting in a less intense color. Light-colored aggregates, such as white sand and crushed limestone, are preferred as they allow the red pigment to express itself more vividly. The size and grading of aggregates also affect the concrete's workability and strength. Aggregates: The type and color of aggregates significantly impact the final appearance.
Clinical Trials: The ultimate goal is to translate the preclinical findings into clinical trials to evaluate the safety and efficacy of Betonred in cancer patients. Phase I trials would focus on assessing safety and determining the optimal dose, while Phase II and Phase III trials would evaluate efficacy in specific types of cancer.
Design Flexibility: betonred (
https://lucrera.com/) can be molded into various shapes and forms, allowing for creative design possibilities. It can be combined with other materials, such as glass, steel, and wood, to create unique architectural features.
It's crucial to work with experienced contractors and use quality control measures to minimize color variations.
Pigment Selection: Choosing the right pigments is critical for long-term colorfastness. Select UV-resistant and chemically stable pigments that are compatible with the cement and other admixtures.
Mix Design: The mix design must be carefully formulated to achieve the desired strength, workability, and color. Variations in cement type, aggregate color, water content, and curing conditions can all affect the final color. Concrete must be kept moist for a sufficient period of time to allow the cement to fully hydrate. It's important to consider the type of cement, aggregates, pigments, and admixtures used.
Curing: Proper curing is essential for achieving optimal strength and durability. Color Consistency: Achieving consistent color throughout a large project can be challenging.
This can be exacerbated by variations in concrete cover or exposure to different environments.
Poor Drainage: Standing water on the concrete surface provides a continuous source of moisture and oxygen, promoting iron oxidation. Insufficient cement content can also reduce the alkalinity of the concrete, compromising the protective layer around reinforcement steel.
Inadequate Curing: Proper curing is essential for hydration of cement and development of a dense, impermeable concrete matrix. Poor Concrete Mix Design: High water-to-cement ratio (w/c) leads to increased porosity and permeability, allowing easier access of moisture and oxygen to the interior of the concrete. They disrupt the passive layer and facilitate the movement of iron ions.
Carbonation: Carbon dioxide from the atmosphere reacts with calcium hydroxide in the concrete, lowering the pH and potentially leading to corrosion of reinforcement.
Aggressive Environments: Exposure to acidic rain, industrial pollutants, or other corrosive substances can damage the concrete surface and promote the formation of iron oxides.
Electrochemical Corrosion: In certain situations, different parts of the steel reinforcement can act as anodes and cathodes, leading to localized corrosion and iron release. Insufficient curing leaves the concrete vulnerable to moisture ingress and carbonation, which can lower the pH and promote corrosion.
Chloride Contamination: Chlorides, often from de-icing salts, marine environments, or contaminated aggregates, are notorious for accelerating corrosion of steel reinforcement.